کولینگ صنعتی به مجموعه فرآیندها و تجهیزاتی اطلاق میشود که برای کاهش دما و کنترل حرارت در محیطهای صنعتی استفاده میشود. این سیستمها به منظور بهبود کارایی تجهیزات، حفظ کیفیت محصولات و جلوگیری از آسیبهای ناشی از گرما در صنایع مختلف مانند تولید، پتروشیمی، و نیروگاهها به کار میروند. کولینگ صنعتی معمولاً شامل برجهای خنککننده، چیلرها و سیستمهای تهویه مطبوع است.
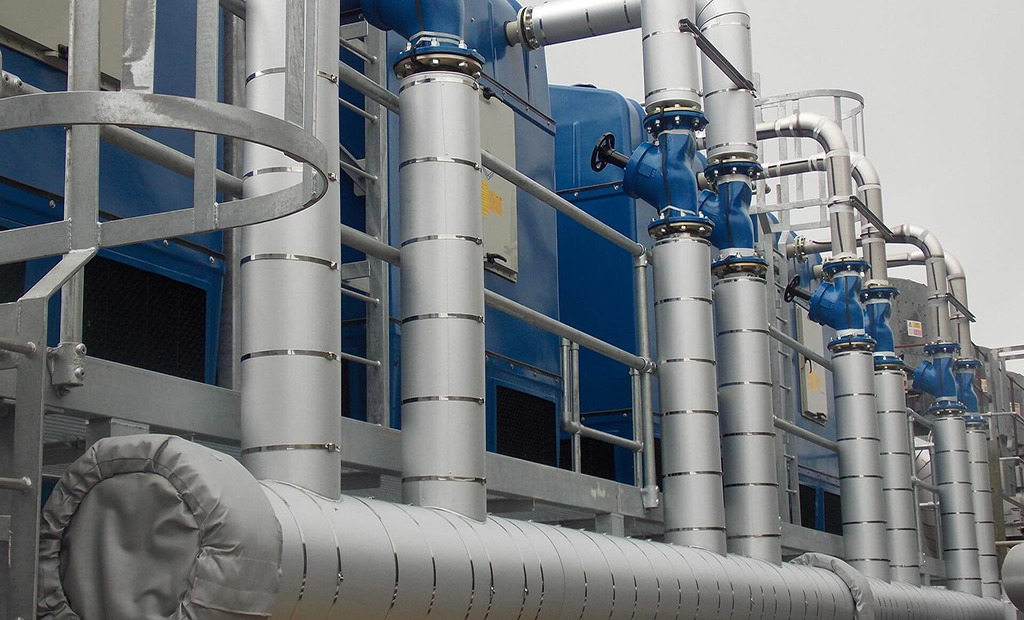
معرفی سیستمهای کولینگ صنعتی
سیستمهای کولینگ صنعتی به مجموعهای از تجهیزات و فناوریها اطلاق میشود که برای کنترل دما و خنکسازی در فرآیندهای صنعتی مورد استفاده قرار میگیرند. این سیستمها به منظور حفظ کیفیت محصولات، افزایش کارایی دستگاهها و جلوگیری از آسیبهای ناشی از دماهای بالا طراحی شدهاند. در ادامه به برخی از انواع سیستمهای کولینگ صنعتی اشاره میشود:
- چیلرها (Chillers): چیلرها دستگاههایی هستند که برای خنکسازی مایعات (عموماً آب) مورد استفاده قرار میگیرند. این مایعات سپس به تجهیزات صنعتی منتقل میشوند تا دما را کنترل کنند.
- سیستمهای تهویه مطبوع (HVAC): این سیستمها به منظور کنترل دما، رطوبت و کیفیت هوا در محیطهای صنعتی و تجاری طراحی شدهاند. آنها شامل تجهیزات خنککننده، گرمایشی و تهویه هستند.
- کولرهای آبی (Evaporative Coolers): این نوع کولرها از تبخیر آب برای خنکسازی هوا استفاده میکنند و در شرایط آب و هوایی خشک و گرم کارایی خوبی دارند.
- سیستمهای خنکسازی با استفاده از آب (Cooling Towers): برجهای خنککننده برای خنکسازی آب گرم خروجی از تجهیزات صنعتی استفاده میشوند. این آب معمولاً در چیلرها یا در فرآیندهای تولید حرارت ایجاد میشود.
- سیستمهای خنکسازی با گاز (Gas Cooling Systems): این سیستمها معمولاً در صنایع خاصی مانند صنایع نفت و گاز و پتروشیمی استفاده میشوند.
- کولرهای صنعتی (Industrial Coolers): این کولرها برای خنکسازی تجهیزات خاصی مانند موتورهای الکتریکی، ژنراتورها و سایر دستگاههای صنعتی طراحی شدهاند.
- سیستمهای کنترل دما (Temperature Control Systems): این سیستمها شامل سنسورها و کنترلکنندههای دیجیتال هستند که به طور خودکار دما را کنترل و تنظیم میکنند.
- سیستمهای خنکسازی غیرمستقیم (Indirect Cooling Systems): در این سیستمها، مایعات خنککننده به صورت غیرمستقیم و از طریق مبدلهای حرارتی دما را کنترل میکنند.
استفاده از این سیستمها به بهینهسازی فرآیندهای صنعتی، افزایش عمر تجهیزات و کاهش مصرف انرژی کمک میکند. انتخاب سیستم مناسب بستگی به نوع صنعت، شرایط محیطی و نیازهای خاص هر کارخانه دارد.
اهمیت کولینگ در صنایع مختلف
کولینگ یا خنکسازی یکی از عوامل کلیدی در عملکرد و بهرهوری صنایع مختلف است. در زیر به برخی از مهمترین جنبههای اهمیت کولینگ در صنایع اشاره میشود:
- حفاظت از تجهیزات: بسیاری از تجهیزات صنعتی مانند موتورها، کمپرسورها و پمپها در صورت دماهای بالا ممکن است دچار آسیب شوند. سیستمهای کولینگ کمک میکنند تا دما در محدوده ایمن نگه داشته شود و از خرابی تجهیزات جلوگیری به عمل آید.
- افزایش بهرهوری: در بسیاری از فرآیندهای صنعتی، دماهای بالا میتوانند باعث کاهش کارایی و بهرهوری شوند. با استفاده از سیستمهای کولینگ، میتوان به بهینهسازی فرآیندها و افزایش کارایی دست یافت.
- کیفیت محصول: در صنایع غذایی، دارویی و شیمیایی، دما نقش مهمی در حفظ کیفیت و بهداشت محصولات دارد. کولینگ مناسب میتواند از فساد، آلودگی و تغییرات کیفیت محصول جلوگیری کند.
- ایمنی: در برخی صنایع، دماهای بالا میتوانند خطرات ایمنی جدی ایجاد کنند. کولینگ مناسب میتواند به کاهش خطرات ناشی از آتشسوزی، انفجار و دیگر حوادث کمک کند.
- کنترل فرآیند: در بسیاری از فرآیندهای صنعتی، نیاز به کنترل دقیق دما وجود دارد. سیستمهای کولینگ به کنترل و تنظیم دما در شرایط مورد نیاز کمک میکنند.
- کاهش هزینهها: با بهینهسازی سیستمهای کولینگ و جلوگیری از خرابی تجهیزات، میتوان هزینههای نگهداری و تعمیرات را کاهش داد.
- محیط زیست: استفاده از سیستمهای کولینگ کارآمد میتواند به کاهش مصرف انرژی و در نتیجه کاهش اثرات منفی بر محیط زیست کمک کند.
به طور کلی، کولینگ در صنایع مختلف نه تنها برای حفظ عملکرد و بهینهسازی فرآیندها ضروری است، بلکه به سلامت و ایمنی کارگران و کیفیت محصولات نیز کمک میکند.
بهینهسازی مصرف انرژی در سیستمهای کولینگ صنعتی
بهینهسازی مصرف انرژی در سیستمهای کولینگ صنعتی یکی از مهمترین چالشها در صنایع مختلف است. این فرآیند میتواند به کاهش هزینهها، افزایش بهرهوری و کاهش اثرات زیستمحیطی کمک کند. در ادامه به چندین روش و تکنیک برای بهینهسازی مصرف انرژی در این سیستمها اشاره میشود:
- بررسی و بهینهسازی طراحی سیستم:
- استفاده از سیستمهای کولینگ با راندمان بالا.
- انتخاب تجهیزات با کیفیت و مناسب که مصرف انرژی کمتری دارند.
- طراحی صحیح شبکههای لولهکشی و کانالها برای کاهش افت فشار.
- کنترل دما و رطوبت:
- استفاده از سنسورها و کنترلرهای پیشرفته برای تنظیم دما و رطوبت به صورت خودکار.
- پیادهسازی سیستمهای کنترل هوشمند که بتوانند به طور بهینه بارهای حرارتی را مدیریت کنند.
- نگهداری و تعمیرات پیشگیرانه:
- انجام تعمیرات منظم و بررسی تجهیزات برای اطمینان از عملکرد بهینه آنها.
- تمیز نگهداشتن فیلترها و کویلها برای جلوگیری از افت کارایی.
- استفاده از منابع انرژی تجدیدپذیر:
- به کارگیری پنلهای خورشیدی یا توربینهای بادی برای تولید انرژی مورد نیاز سیستمهای کولینگ.
- استفاده از انرژی زمینگرمایی در سیستمهای تهویه مطبوع.
- بهرهوری حرارتی:
- استفاده از سیستمهای بازیافت حرارت که میتواند حرارت اضافی را از فرآیندها جمعآوری و برای گرمایش سایر بخشها استفاده کند.
- نصب چیلرهای با راندمان بالا و سیستمهای کندانسور بهینه.
- آموزش پرسنل:
- آموزش کارکنان در زمینه بهینهسازی مصرف انرژی و اهمیت آن.
- تشویق به استفاده از روشهای صرفهجویی انرژی در کارهای روزمره.
- تحلیل دادهها و بازخورد:
- استفاده از نرمافزارهای مدیریت انرژی برای پایش و تحلیل مصرف انرژی.
- شناسایی نقاط ضعف و فرصتهای بهینهسازی از طریق دادههای جمعآوری شده.
- استفاده از تکنولوژیهای جدید:
- بررسی و پیادهسازی تکنولوژیهای نوین مانند کولینگ تبخیری، کولرهای جذبی و … که میتوانند مصرف انرژی را کاهش دهند.
با پیادهسازی این راهکارها، صنایع میتوانند به بهینهسازی مصرف انرژی در سیستمهای کولینگ خود بپردازند و به اهداف اقتصادی و زیستمحیطی خود نزدیکتر شوند.
نگهداری و تعمیرات سیستمهای کولینگ
نگهداری و تعمیرات سیستمهای کولینگ (سیستمهای خنککننده) برای حفظ کارایی و طول عمر این سیستمها بسیار حائز اهمیت است. در ادامه، به برخی از نکات کلیدی در این زمینه اشاره میشود:
1. نظافت منظم
- فیلترها: فیلترهای هوا باید به طور منظم تمیز یا تعویض شوند. فیلترهای کثیف میتوانند جریان هوا را مسدود کرده و کارایی سیستم را کاهش دهند.
- کوئلها و کندانسورها: شستشوی منظم کوئلها و کندانسورها از گرد و غبار و آلودگیها به بهبود کارایی سیستم کمک میکند.
2. بررسی نشتیها
- نشتی گاز مبرد میتواند به کاهش کارایی سیستم و افزایش هزینهها منجر شود. لذا باید به طور دورهای نشتیها بررسی و در صورت نیاز تعمیر شوند.
3. کنترل دما و فشار
- بررسی و تنظیم دما و فشار سیستم به منظور اطمینان از عملکرد بهینه آن بسیار مهم است.
4. بررسی الکتریکی
- اتصالات الکتریکی و موتورهای فن باید به طور منظم بررسی شوند. اتصالات شل یا معیوب میتوانند باعث خرابی سیستم شوند.
5. تست عملکرد
- سیستم باید به طور دورهای تست عملکرد شود تا از کارایی آن اطمینان حاصل شود. این تست شامل بررسی صداها، لرزشها و عملکرد کلی سیستم است.
6. برنامهریزی تعمیرات پیشگیرانه
- ایجاد یک برنامه منظم برای تعمیرات پیشگیرانه میتواند به جلوگیری از خرابیهای بزرگ و هزینهبر کمک کند.
7. آموزش کارکنان
- آموزش کارکنان در زمینه استفاده و نگهداری صحیح از سیستمهای کولینگ میتواند به افزایش عمر مفید تجهیزات کمک کند.
8. استفاده از تکنولوژیهای نوین
- استفاده از سیستمهای هوشمند و سنسورهای پیشرفته میتواند به کنترل بهتر و بهینهسازی مصرف انرژی کمک کند.
با رعایت این نکات و انجام نگهداریهای منظم، میتوان عملکرد سیستمهای کولینگ را بهینه کرده و از بروز مشکلات جدی جلوگیری کرد.
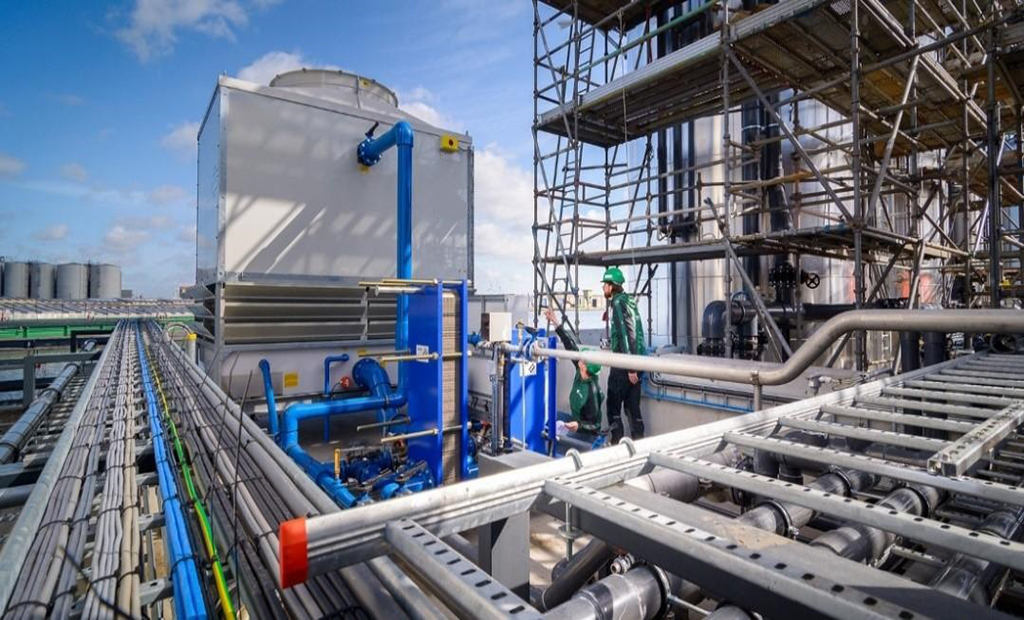
تأثیر تغییرات اقلیمی بر سیستمهای کولینگ صنعتی
تغییرات اقلیمی تأثیرات قابل توجهی بر سیستمهای کولینگ صنعتی دارند. این تأثیرات میتوانند به شکلهای مختلفی بروز کنند:
- افزایش دما: با افزایش دماهای میانگین جهانی، نیاز به سیستمهای کولینگ در صنایع بیشتر میشود. این افزایش دما میتواند منجر به افزایش مصرف انرژی و هزینههای عملیاتی گردد.
- تغییر الگوهای بارش: تغییرات در الگوهای بارش میتواند تأثیرات مستقیمی بر تأمین آب مورد نیاز برای سیستمهای کولینگ داشته باشد. کاهش بارش میتواند به کمبود آب و افزایش هزینهها منجر شود.
- افزایش رطوبت: در برخی مناطق، افزایش رطوبت میتواند کارایی سیستمهای کولینگ را تحت تأثیر قرار دهد. سیستمهای خنککننده ممکن است در شرایط رطوبت بالا کارایی کمتری داشته باشند.
- تأثیر بر تجهیزات: تغییرات اقلیمی میتواند به آسیبهای فیزیکی به تجهیزات کولینگ منجر شود. به عنوان مثال، طوفانها و سیلابها میتوانند به زیرساختها آسیب برسانند.
- تنظیمات قانونی و استانداردها: با توجه به تغییرات اقلیمی، ممکن است قوانین و استانداردهای جدیدی برای کاهش مصرف انرژی و بهبود کارایی سیستمهای کولینگ وضع شود. این مسئله میتواند نیاز به سرمایهگذاریهای جدید و تغییر در طراحی سیستمها را به همراه داشته باشد.
- نیاز به فناوریهای پایدار: به دلیل تغییرات اقلیمی، صنایع به سمت استفاده از فناوریهای پایدار و انرژیهای تجدیدپذیر برای تأمین نیازهای کولینگ خود حرکت میکنند. این تغییرات میتوانند شامل استفاده از سیستمهای خنککننده با کارایی بالا و استفاده از منابع آب بارانی باشند.
- تأثیر بر زنجیره تأمین: تغییرات اقلیمی میتواند بر زنجیره تأمین مواد اولیه و تجهیزات مورد نیاز برای سیستمهای کولینگ تأثیر بگذارد و منجر به نوسانات قیمت و تأخیر در تحویل شود.
به طور کلی، تغییرات اقلیمی چالشهای متعددی را برای سیستمهای کولینگ صنعتی ایجاد میکند و نیاز به استراتژیهای جدید و نوآورانه برای مدیریت و بهینهسازی این سیستمها را افزایش میدهد.
فناوریهای نوین در کولینگ صنعتی
فناوریهای نوین در کولینگ صنعتی (سیستمهای خنککننده صنعتی) بهطور مستمر در حال توسعه و بهبود هستند. این فناوریها به منظور افزایش کارایی، کاهش مصرف انرژی و به حداقل رساندن تأثیرات زیستمحیطی طراحی شدهاند. در زیر به برخی از این فناوریها اشاره میشود:
- سیستمهای خنککننده مبتنی بر تبخیر: این سیستمها از تبخیر آب برای خنک کردن استفاده میکنند و میتوانند مصرف انرژی را به طور قابل توجهی کاهش دهند.
- کولرهای هیبریدی: این سیستمها ترکیبی از روشهای خنککننده مختلف (مانند تبخیری و مکانیکی) هستند و میتوانند به صورت هوشمند عمل کنند تا بهترین روش خنکسازی را انتخاب کنند.
- فناوریهای خنککننده با استفاده از انرژی خورشیدی: این فناوریها به استفاده از پنلهای خورشیدی برای تأمین انرژی مورد نیاز سیستمهای خنککننده میپردازند.
- سیستمهای خنککننده مبتنی بر گاز: این فناوریها از گازهای طبیعی و یا گازهای دیگر برای خنک کردن استفاده میکنند و میتوانند به کاهش انتشار گازهای گلخانهای کمک کنند.
- فناوریهای نوین کنترل هوشمند: استفاده از سنسورها و نرمافزارهای هوشمند برای کنترل دما و رطوبت به صورت بهینه، به کاهش مصرف انرژی و افزایش کارایی کمک میکند.
- پمپهای حرارتی: این سیستمها میتوانند به عنوان یک منبع خنکی و همچنین به عنوان یک منبع گرما عمل کنند، که باعث افزایش کارایی و کاهش هزینهها میشود.
- فناوریهای نانو: استفاده از مواد نانو برای بهبود انتقال حرارت و کاهش وزن سیستمهای خنککننده در حال بررسی و توسعه است.
- خنککنندههای بدون فریون: این فناوریها به دنبال جایگزینی مواد مضر با مواد سازگار با محیط زیست هستند و میتوانند به کاهش اثرات زیستمحیطی کمک کنند.
استفاده از این فناوریها میتواند به صنایع کمک کند تا بهرهوری بیشتری داشته باشند و در عین حال تأثیرات منفی بر روی محیط زیست را کاهش دهند.
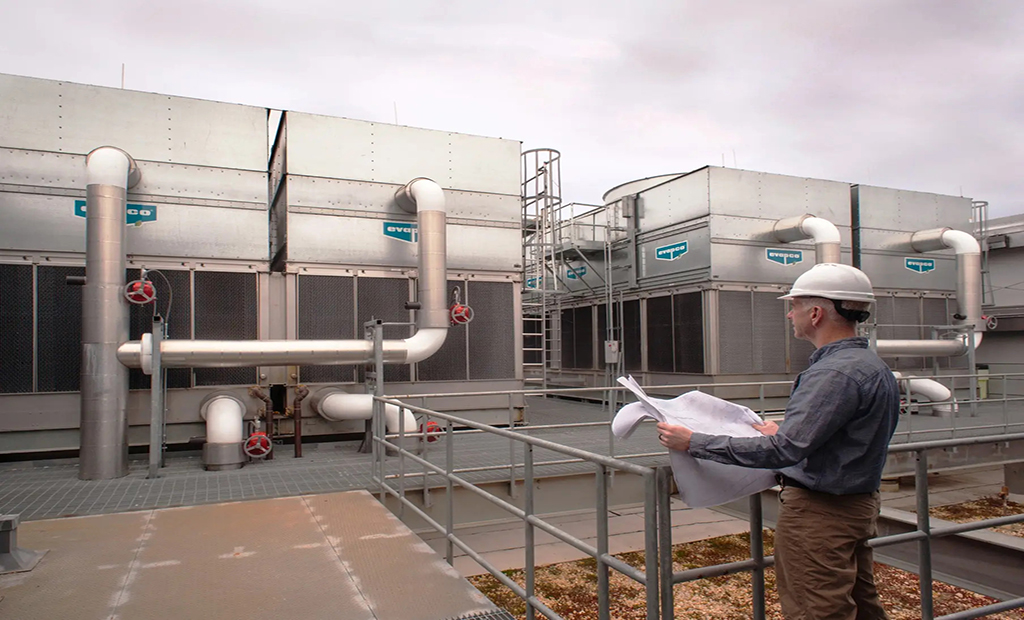
تحلیل هزینه-فایده سیستمهای کولینگ
تحلیل هزینه-فایده سیستمهای کولینگ (سیستمهای خنککننده) یک ابزار مهم برای ارزیابی اقتصادی و عملیاتی پروژهها و سرمایهگذاریها در این حوزه است. این تحلیل به کمک آن میتوان مزایا و معایب مختلف سیستمهای کولینگ را بررسی و تصمیمات بهتری اتخاذ کرد. در ادامه، مراحل و عوامل کلیدی در تحلیل هزینه-فایده سیستمهای کولینگ آورده شده است:
1. تعریف اهداف و نیازها
- تعیین نیازهای خنککنندگی (مثلاً برای یک ساختمان، کارخانه یا تجهیزات خاص)
- شناسایی معیارهای عملکردی و کیفیتی مورد نظر
2. شناسایی انواع سیستمهای کولینگ
- سیستمهای کولینگ مرکزی
- سیستمهای کولینگ محلی (اسپلیت، پنجرهای و …)
- کولرهای آبی
- چیلرها و برجهای خنککننده
3. محاسبه هزینهها
- هزینههای اولیه: شامل خرید تجهیزات، نصب و راهاندازی
- هزینههای عملیاتی: شامل انرژی مصرفی، نگهداری و تعمیرات
- هزینههای غیرمستقیم: مانند هزینههای مرتبط با عدم فعالیت تجهیزات در صورت خرابی
4. تحلیل منافع
- کاهش دما و بهبود شرایط کاری: مزایای مربوط به افزایش بهرهوری کارکنان و کاهش استرس گرمایی
- افزایش عمر تجهیزات: جلوگیری از آسیبهای ناشی از دماهای بالا
- کاهش مصرف انرژی: در سیستمهای بهینه، کاهش هزینههای انرژی
5. تحلیل دوره بازگشت سرمایه (ROI)
- محاسبه زمان لازم برای بازگشت سرمایه از طریق صرفهجوییهای ناشی از استفاده از سیستم کولینگ
- مقایسه با سایر گزینههای موجود
6. تحلیل ریسکها
- شناسایی ریسکهای مرتبط با نصب و استفاده از سیستمهای کولینگ
- ارزیابی تأثیرات احتمالی بر عملکرد و هزینهها
7. جمعبندی و تصمیمگیری
- تجزیه و تحلیل نهایی هزینهها و منافع
- ارائه پیشنهادات و توصیهها برای انتخاب بهترین سیستم کولینگ بر اساس تحلیل انجام شده
نتیجهگیری
تحلیل هزینه-فایده سیستمهای کولینگ به مدیران و تصمیمگیرندگان کمک میکند تا انتخابهای بهینهتری داشته باشند و از منابع مالی به بهترین شکل ممکن استفاده کنند. در این راستا، توجه به جنبههای محیط زیستی و صرفهجویی در مصرف انرژی نیز از اهمیت بالایی برخوردار است.
برای خواندن بقیه مطالب به وبلاگ لوتوس فن مراجعه فرمایید.
بدون دیدگاه